When to use a safety relief valve or a rupture disc
RELIEF VALVE or RUPTURE DISC – What is right for your sanitary process?
Keeping people and processes safe from overpressure events is extremely important in manufacturing facilities. In certain situations, designers are required to specify safety mechanisms to relieve pressure if overpressure occurs. Rupture discs and safety relief valves are both used for this purpose.
What is a rupture disc?
A rupture disc, sometimes called a bursting disc, is a safety device that protects piping, vessels, and other equipment from excessive pressure or vacuum. It is a thin slice of metal that has been scored in order to burst at a predefined pressure, releasing pressure to prevent injury or damage. By definition, a rupture disc is a one-time use safety device.
What is a safety relief valve?
A safety relief valve or pressure relief valve is a type of safety valve used to control or limit the pressure in a system. Pressure might otherwise build up and create a process upset, instrument or equipment failure or fire. The obvious difference between a relief or safety valve and a rupture disc is that the valve reseats and the disc does not.
Pros and cons of using a safety relief valve versus a rupture disc
On the pro side, a rupture disc can be purchased at a lower price point and is a smaller, more compact device compared to a safety relief valve. Cons for the rupture disc are that once it ruptures, it breaks into pieces and its useful life is over. Fragments could harm the equipment and process media can be exposed to the atmosphere. The process comes to a stop until a new rupture disc is procured and installed. It is a good candidate for rare, sudden overpressure events where equipment downtime is not a concern.
The advantage to choosing a safety relief valve is that it is reusable. While the initial capital outlay is higher, the useful life is usually longer. A safety relief valve is designed to relieve excess pressure, reseat, and return to service once normal conditions have been restored. A safety relief valve can minimize damage to other system components.
Sanitary Safety Relief Valves for biopharma applications
Steriflow Valve makes a sanitary safety relief valve National Board Certified to ASME VIII/XIII for overpressure protection. They are designed for the same purpose as a standard safety relief valve but have sanitary specifications for biopharma applications.
The Steriflow Sanitary Safety Relief Valves (SSRV Series) are designed to relieve over-pressure activity in hygienic and aseptic processes and clean utility systems. They are manually set to open at a predetermined pressure and re-seat after pressure subsides. This protects pressure vessels and other equipment from pressure that exceeds their design limits.
Specific sanitary features include high cleanability (L/D < 1.5); 20 Ra µin (0,5 Ra µm); Electropolished surfaces; FDA and USP Class VI wetted parts; optional manual or pneumatic lift device for Clean-in-Place; Bellows seal that isolates process from valve internals on some models.
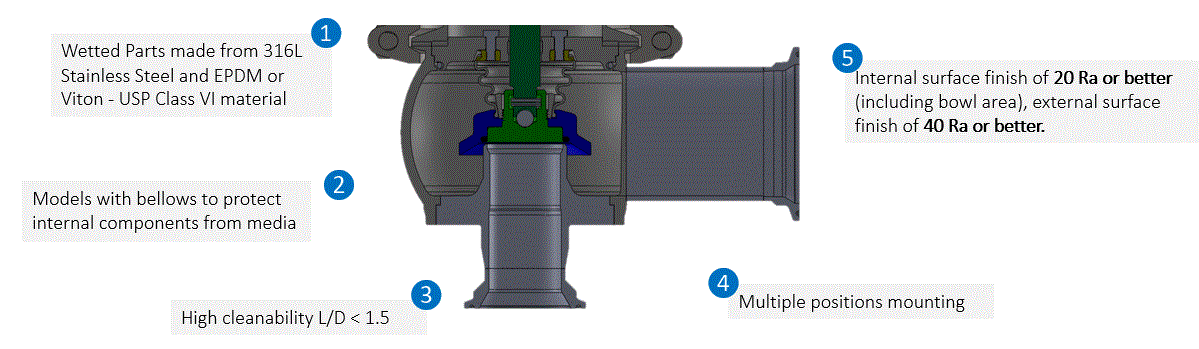
Applications where SSRV safety relief valves are used include:
- Single use or stainless steel vessel pressure relief
- Clean air and gas point-of-use (POU) pressure relief
- Lyophilizer clean steam pressure relief
- Bioreactor – fermenter vessel and vessel jackets
- Formulation and other pharma process vessels
- Clean steam systems
- WFI and USP PW vessels
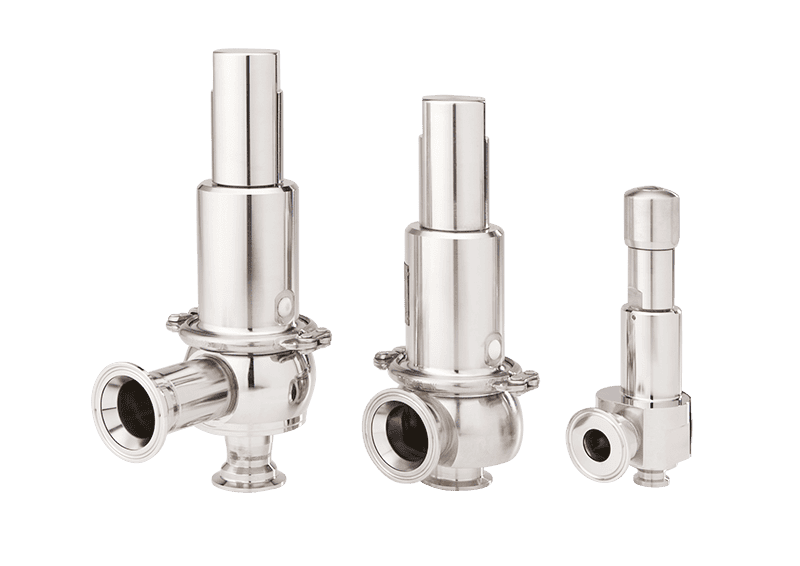
Are you considering overpressure control for your sanitary process? View our SSRV product Line for specifications and certifications.
How Can We Help You With Your Sanitary Processes?
Contact us to learn more about how an SSRV can protect your sanitary process