New Solutions For SIP Design For Larger Vessels
A product designed for vessel drains can simplify vessel drain piping, improve SIP heat up time and efficiency and lower CAPex.
There are 2 problems associated with conventionally designed large vessel SIP drains.
- Inefficient use of clean steam and slow heat-up
- High initial capital cost
This is a conventional piping design for validated vessel drains.
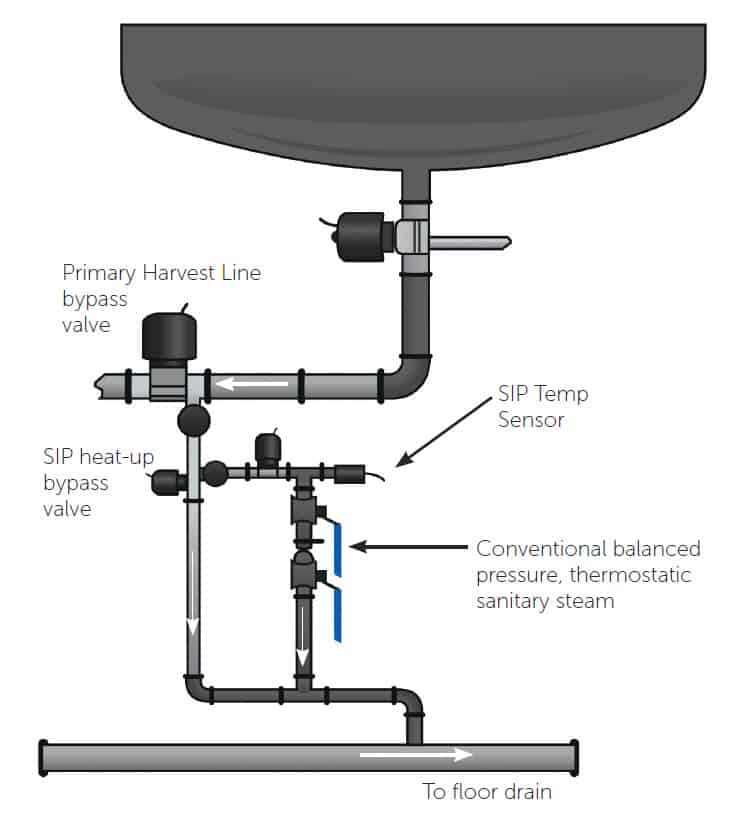
Heat-up:
- During SIP heat-up, air and condensate (and clean steam) are diverted through the harvest line 3-way bypass valve directly to drain
Temperature Maintenance:
- When the SIP temperature sensor reaches ~203°F (~95°C), the bypass valve opens to direct the lighter condensate load through the steam traps. Actual temperature depends upon DCS/PLC configuration.
Note: during sanitization (pre SIP), Rinse and CIP, liquids are usually diverted through the primary harvest line 3-way bypass valve directly to drain. Though some end users divert through a secondary harvest line 3-way bypass valve further downstream.
Several years ago, Steriflow looked at the problems associated with the conventional piping design, and started work on a design to alleviate those problems. We developed a trap with enough capacity to handle most rinse/CIP/rinse sanitization flows and the air and condensate flows associated with SIP.
We did it by developing the world’s first dual element trap. It works in the following manner:
Two bellows assemblies work together to handle sanitization liquids (rinse/CIP/rinse), and the heat-up and maintenance loads of larger vessels.
- During SIP, both bellows are open during heat-up providing excellent capacity for eliminating air and condensate.
- The higher capacity bellows is designed to close when vessel temperature is between 203°F and 212°F (90°C and 100°C). This allows the lower subcooling MK93 bellows to handle the smaller loads generated during temperature maintenance.
- No clean steam is lost during operation of the trap. Both bellows will close when the bellows sense saturated steam temperatures.
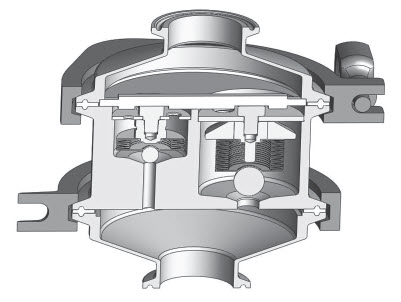
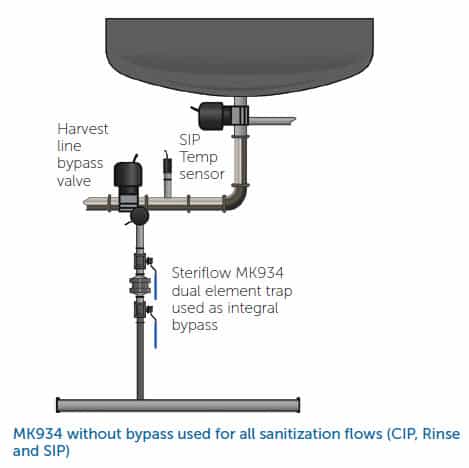
Benefits:
- CAPex: Approximately $2800 less to construct than the traditional piping arrangement
- Heat-up time improvement: NO lost clean steam – an enthalpy from entering steam heats the vessel, none lost to drain
- OPex: Less clean steam used than with traditional piping arrangement
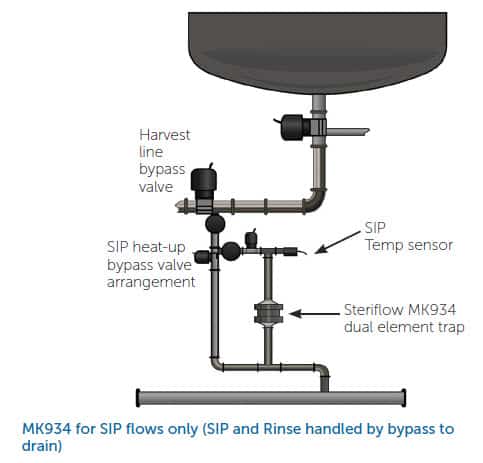
Benefits:
- CAPex: None. Cost approximately $300 more than the traditional piping arrangement
- Heat-up time improvement: NO lost clean steam – all enthalpy from entering steam heats the vessel, none lost to drain
- OPex: Less clean steam used than with traditional piping arrangement
Subscribe to Steriflow's Blog!
Be one of the first to watch new how-to videos, read published articles, and hear from experts about all things related to sanitary processing systems.